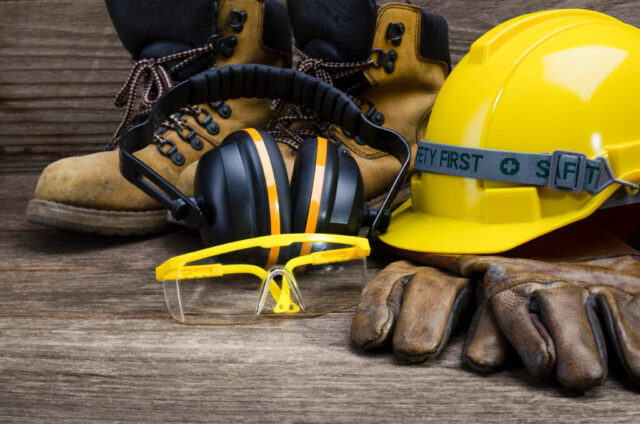
Personal Protective Equipment, commonly known as PPE, plays an essential role in ensuring the safety and well-being of individuals working in environments with potential hazards.
A PPE kit is not just a collection of safety gear; it’s a frontline defense mechanism that protects workers from risks ranging from chemical exposure to airborne pathogens, sharp objects, and extreme temperatures. As industries expand and workplaces evolve, the demand for reliable protective equipment continues to grow.
Across sectors like healthcare, construction, manufacturing, and laboratory science, PPE is not optional. Regulations and safety protocols often mandate its use, emphasizing the responsibility of employers to provide the proper gear. A PPE kit is typically assembled to suit the specific risks of a worksite or profession, combining items such as gloves, face masks, goggles, coveralls, and footwear. Its purpose is to reduce direct contact with harmful substances and prevent injuries from occurring.
The importance of these kits became especially evident during global health crises when protective gear was essential for frontline workers. However, the relevance of a PPE kit goes far beyond emergency situations. In daily operations, it ensures consistent safety standards, minimizes downtime caused by accidents, and supports a workplace culture focused on health and responsibility. With the right equipment, employees can perform their duties confidently, knowing their protection is prioritized.
The Role of PPE in Hazard Control
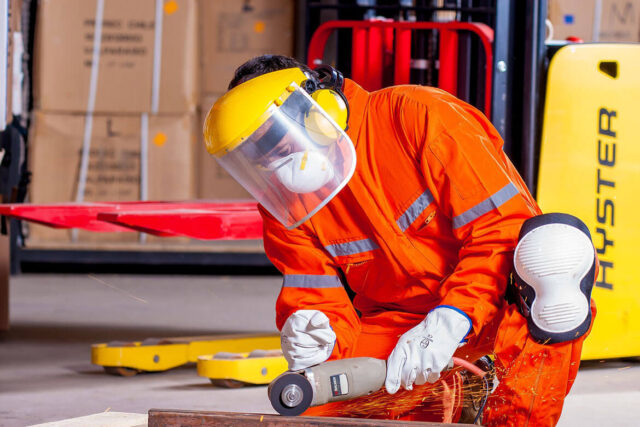
Workplace hazards come in various forms, and no single piece of equipment can address them all. A PPE kit is tailored to protect against specific risks identified through hazard assessments. In environments where workers are exposed to chemicals, protective gloves, eye shields, and respirators may be included. For jobs involving heavy machinery or construction, hard hats, steel-toe boots, and high-visibility vests become necessary. By equipping workers with what they need, employers demonstrate a commitment to reducing accidents and maintaining productivity.
In industrial settings, airborne particles can cause long-term respiratory problems. A PPE kit designed for such environments often includes a dust mask or respirator that filters out dangerous substances. Similarly, in settings where loud noise is a constant factor, ear protection must be provided to prevent hearing loss over time. These elements are not arbitrary additions; they’re the result of careful planning based on the actual risks present.
The effectiveness of a PPE kit depends not only on its contents but also on proper usage. Protective gear must fit correctly, be worn consistently, and be maintained to remain effective. Disposable items must be replaced regularly, while reusable gear should be cleaned and inspected for signs of wear. Staff training plays a vital role in this process. Employees must understand not only how to use the equipment but walso hy each piece matters. This fosters accountability and ensures safety protocols are taken seriously.
A PPE kit also supports compliance with health and safety regulations. Occupational safety agencies often conduct inspections to verify that protective measures are in place. Having properly stocked and maintained PPE on hand helps businesses avoid penalties and ensures continuity of operations. More importantly, it protects lives by creating a barrier between the worker and potential harm.
Adapting PPE Kits to Different Industries
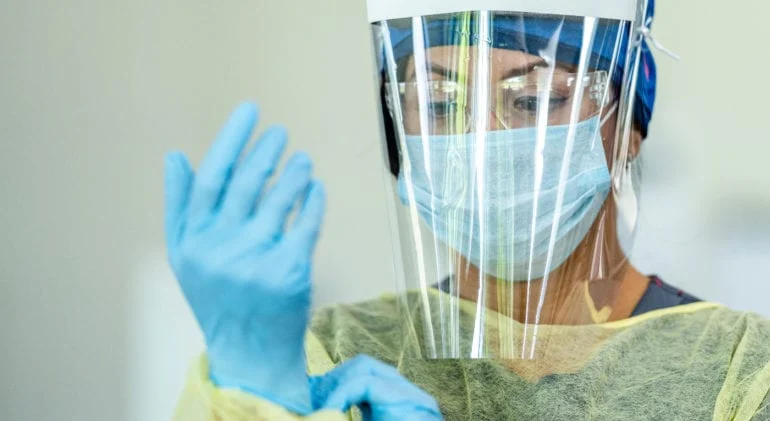
While the concept of PPE remains consistent across industries, the specific configuration of a PPE kit can vary dramatically. In the medical field, the focus is often on infection prevention. Gloves, gowns, face shields, and N95 respirators are commonly included to protect healthcare providers from patient-transmitted illnesses. These kits are designed for use in sterile environments, and often include single-use components that reduce the risk of cross-contamination.
In contrast, construction sites demand rugged gear that can withstand physical stress. A PPE kit for this environment would likely feature hard hats, safety harnesses, eye protection, and boots designed to guard against impact injuries and falls. These kits must meet rigorous safety standards and be regularly evaluated for compliance with industry regulations.
Laboratory workers face risks from exposure to chemical spills, heat sources, or sharp instruments. A standard PPE kit in this field may include lab coats, safety goggles, chemical-resistant gloves, and flame-retardant clothing. These items protect not only the worker but also help contain potential contamination that could compromise research or cause harm to others.
Even office settings may require specialized PPE during certain conditions. During times of viral outbreaks, for example, a PPE kit might be distributed to administrative staff and guests, including hand sanitizer, face masks, and disinfectant wipes. While the level of protection might not be as extensive as in high-risk environments, the purpose remains the same, to prevent harm and promote safety.
What unifies all these uses is the principle that no task should proceed without appropriate protection. Tailoring each PPE kit to the job helps eliminate gaps in safety measures and ensures that every worker, regardless of role, is considered in the overall risk management strategy.
Proper Maintenance and Storage of PPE Kits
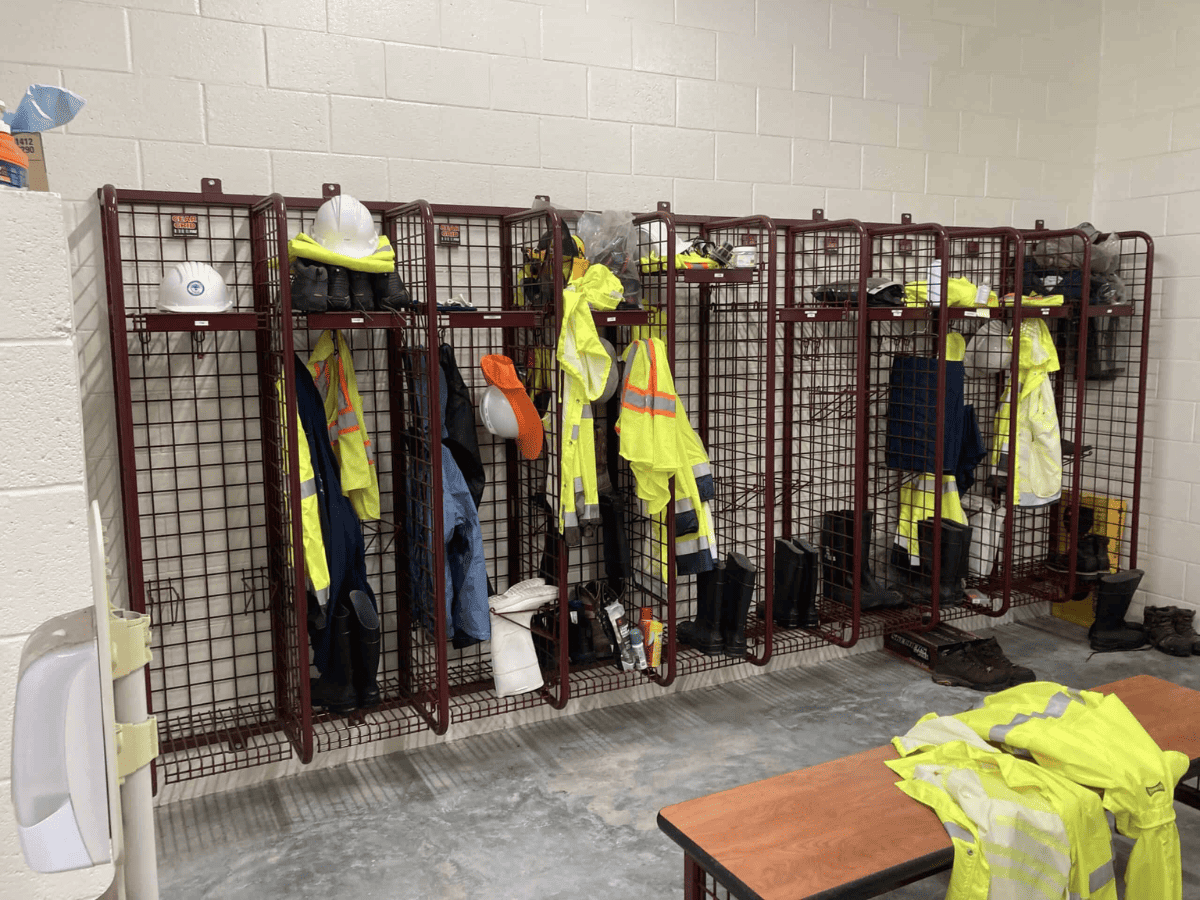
To retain their effectiveness, PPE kits must be stored properly and maintained with care. Items like gloves and masks have expiration dates or can degrade over time if exposed to heat, moisture, or sunlight. Designating secure, climate-controlled storage areas helps prolong the life of the equipment and keeps it in ready-to-use condition.
Each piece of gear should be inspected before use. Damaged, frayed, or compromised equipment must be discarded and replaced without delay. Employers often implement checklists or inventory systems to keep track of PPE availability, usage patterns, and reorder needs. These systems are essential for ensuring that kits remain fully stocked and ready for any task or emergency.
A PPE kit must also be aligned with changing workplace conditions. As tasks evolve or new risks emerge, gear may need to be updated or supplemented. Regular safety audits and communication with employees help ensure that protective equipment meets current needs. Encouraging feedback from the workforce can also uncover overlooked issues or opportunities for improved protection.
Training is a continuous process. Staff should be reminded of proper usage techniques and the reasons behind them. This helps prevent complacency and encourages consistent adherence to safety practices. New hires, in particular, must be oriented on the importance of the PPE kit from day one, integrating its use into daily operations rather than treating it as an afterthought.
Promoting a Culture of Protection and Preparedness
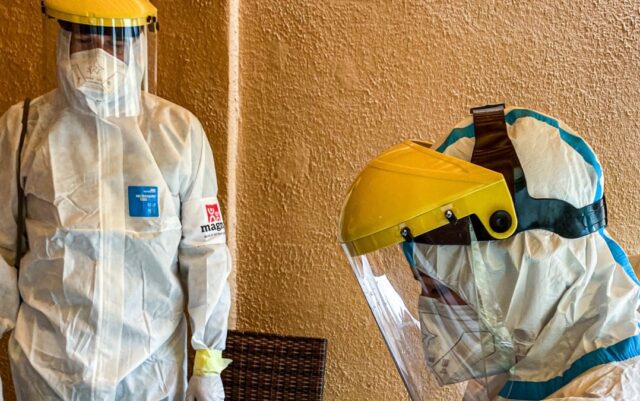
The PPE kit is more than a safety measure, it is a symbol of a workplace culture that values health, responsibility, and preparation. By ensuring that each employee has access to the correct protective gear, businesses show that they are not only meeting legal obligations but also respecting the individuals who power their operations.
A well-prepared team works with greater confidence and efficiency. Knowing that they are protected from foreseeable hazards allows employees to focus on their tasks without fear or distraction. This in turn supports higher morale, lower injury rates, and stronger organizational performance.
Every industry faces unique challenges, but the principles of protection are universal. As businesses navigate evolving risks and workplace demands, the PPE kit remains a fundamental tool in building safer, more resilient operations.